TQC
Cheerme Office Booth Quality Control System
Quality is not just a promise, it's the essence of our daily operations. We maintain strict control over every detail of our office booth production process. From our single work pod to double work pod and 4 to 6 people work pods, we’re ensuring that each step is performed to the highest standard. Over time, our techniques are refined and our quality management system becomes stronger. We believe that through relentless effort and continuous improvement, the quality of our phone booth series will always remain ahead.
Quality Manual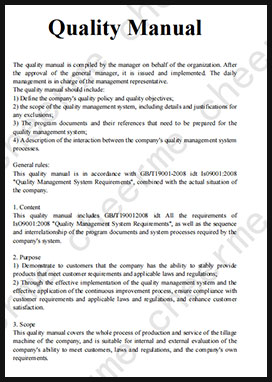
Cheerme Office Booth Flow of Production and Analysis of Quality Control Process
In our pursuit of manufacturing excellence, we implement strict quality controls throughout every step of production. Each Cheerme office booth undergoes quality checks starting from the arrival of raw materials at the factory. Below, we will examine the critical aspects of our manufacturing process that work together to ensure the superior performance and consistently high standards of our products.
Firstly let's start with a quick overview of the various steps of quality control from the flow of production.
Firstly let's start with a quick overview of the various steps of quality control from the flow of production.
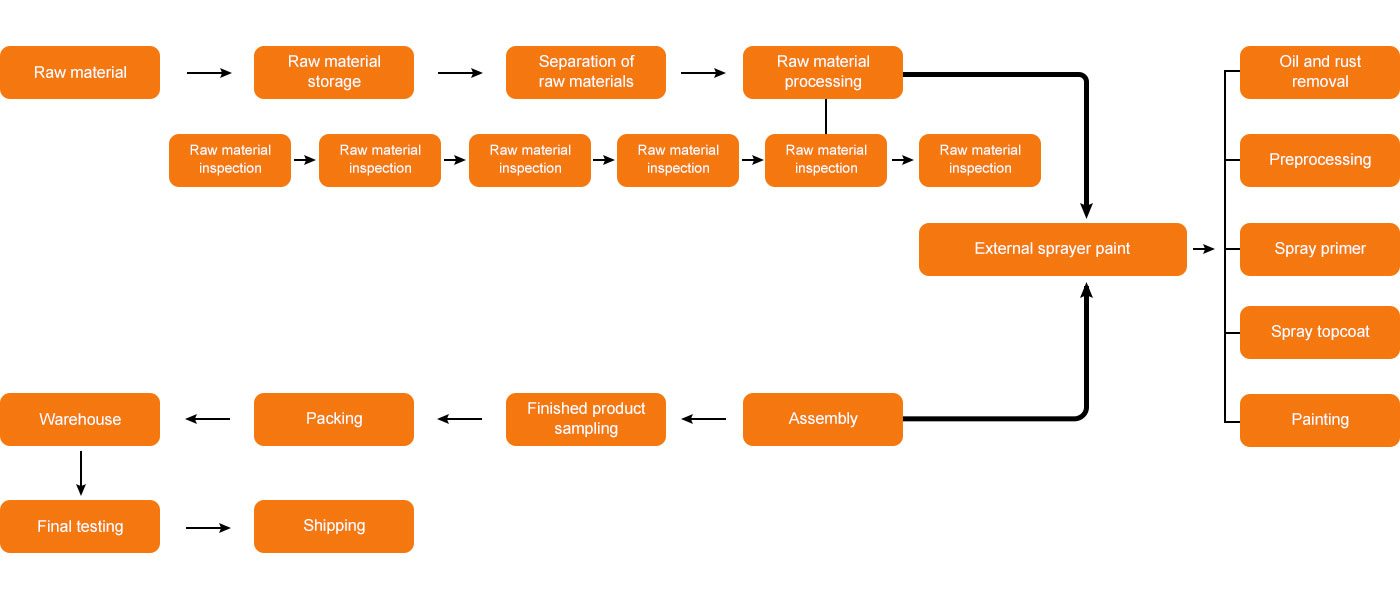
1.Raw Material Inspection:
The first step is to assess the quality of incoming materials to ensure they meet the predefined standards before processing.
Our soundproof booth’s raw materials are: steel panel, Acoustic panel,6063 aluminum alloy, 4mm polyester fiber sound insulation panels, 9mm polyester fiber,tempered glass, PP plastic,tiger brand powder and Gabriel fabric etc.
All these are 100% environmentally friendly materials which got certified.Our soundproof booth’s raw materials are: steel panel, Acoustic panel,6063 aluminum alloy, 4mm polyester fiber sound insulation panels, 9mm polyester fiber,tempered glass, PP plastic,tiger brand powder and Gabriel fabric etc.
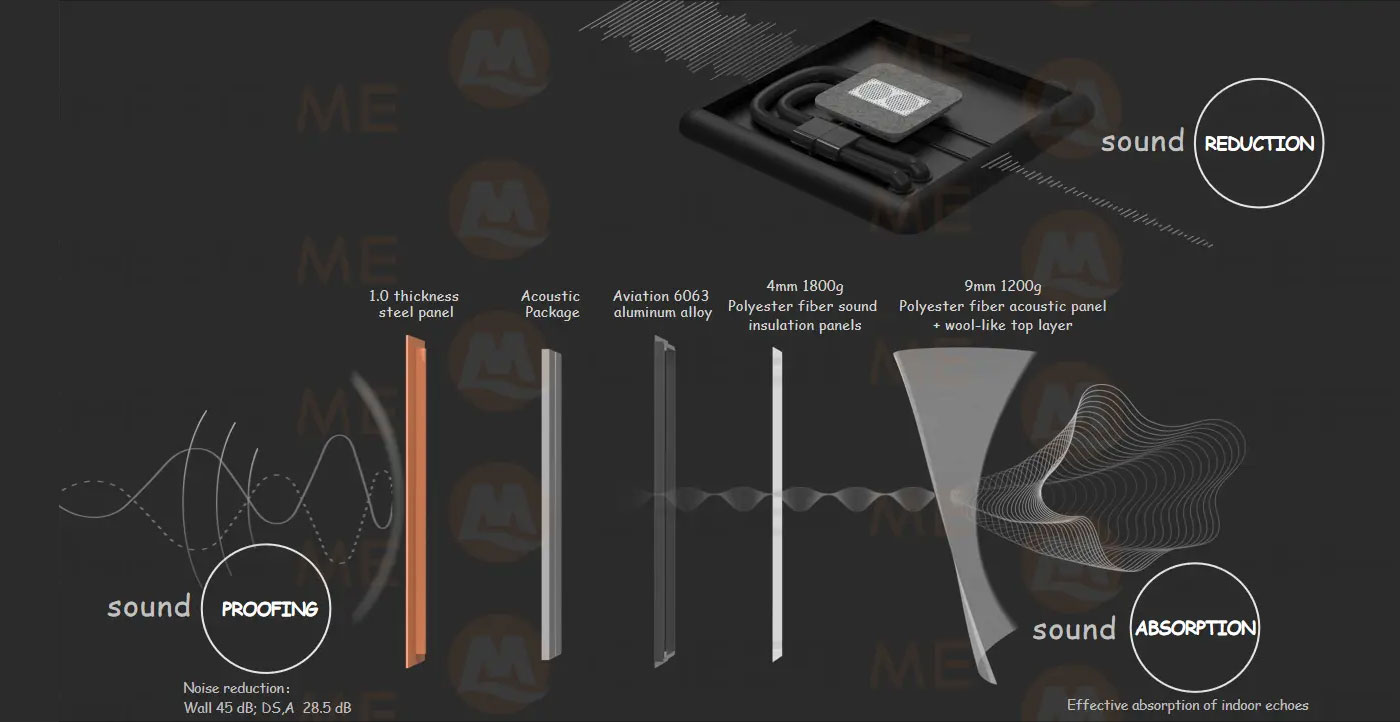
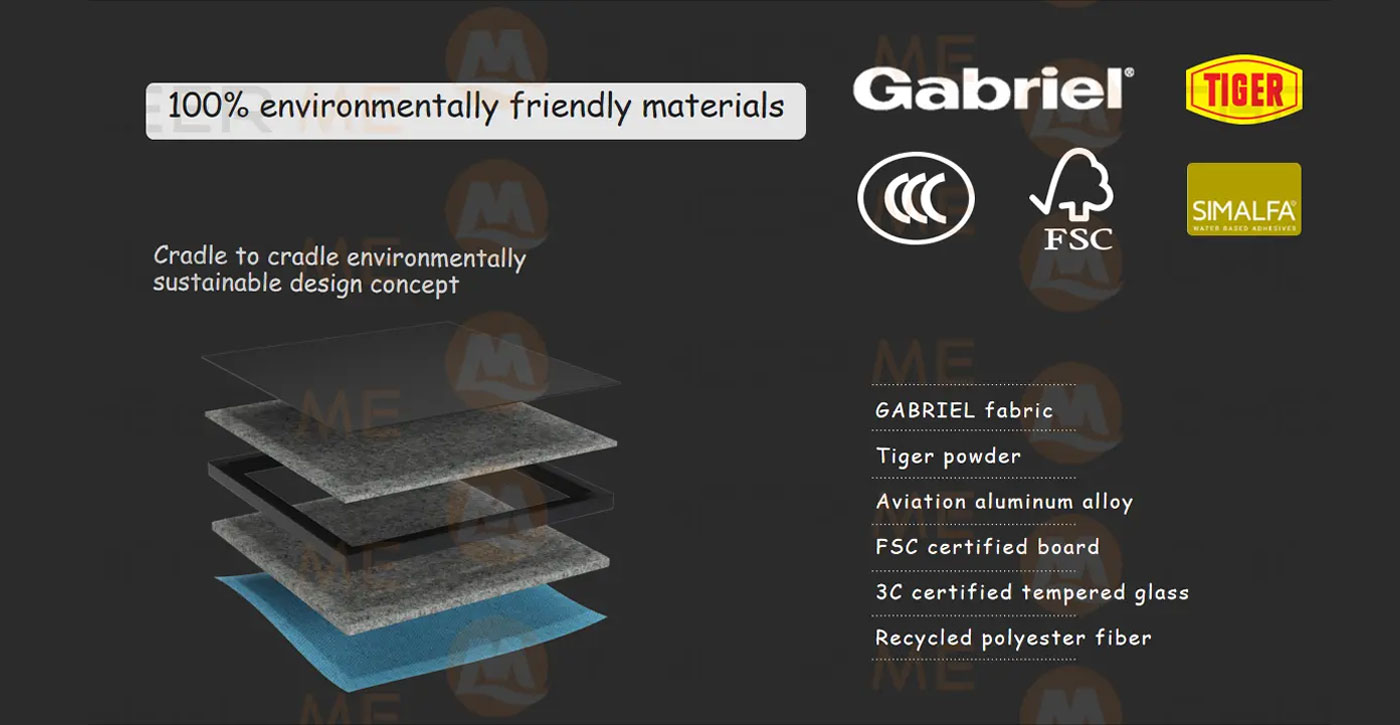
Office booth’s raw material inspection is a critical first step in the production process. Its purpose is to ensure that all incoming materials meet production standards. We screen the booth raw materials for conformity through a series of inspection procedures, including chemical analysis, mechanical testing, and dimensional accuracy measurements. Ensuring the quality of the final product is not the only concern, as production efficiency and product reliability are also impacted. This step involves identifying and rejecting any unqualified raw materials to prevent them from entering the next production stage.
In the Raw Material Processing stage, we utilize various techniques to transform raw materials into product components.
In the Raw Material Processing stage, we utilize various techniques to transform raw materials into product components.
2.Raw Material Storage:
Systematically store inspected raw materials of Cheerme office booth to maintain their quality and ensure production efficiency.
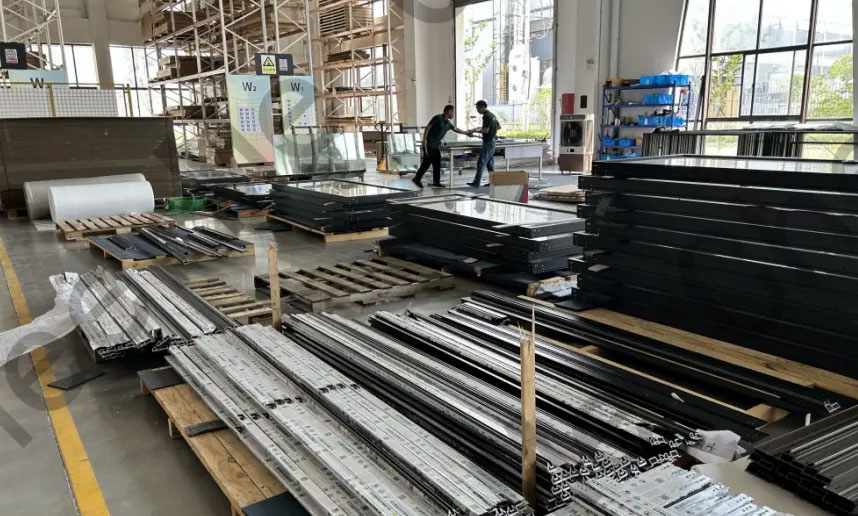
3.Separation of Raw Material:
Raw materials are categorized based on production needs to prepare them for processing operations.
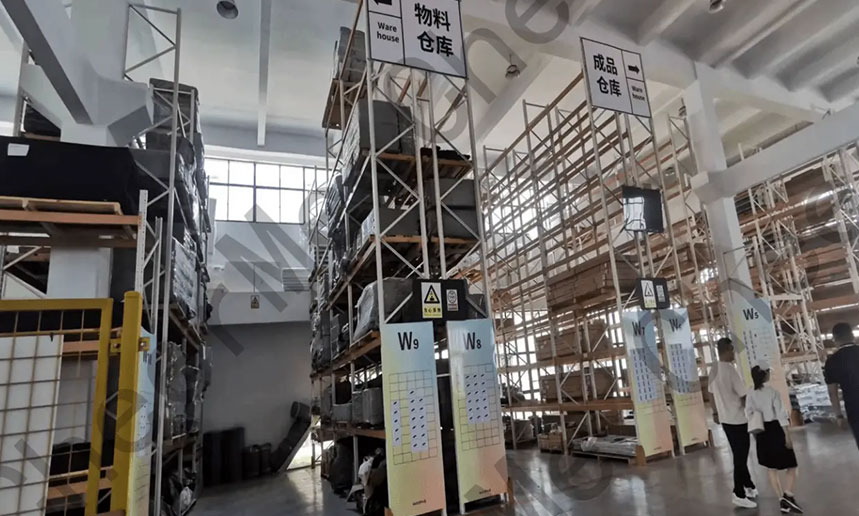
4.Raw Material Processing:
Various processing techniques, such as punching and laser cutting, transform Cheerme office booth’s raw materials into components of the final product.
Soundproof booth’s laser cutting, which utilizes high-precision technology to provide fine and intricate cuts.
Bending to shape materials to meet design requirements, and welding to fuse different metal parts together to create a strong structure.
Polishing is the process of grinding and smoothing metal surfaces to improve their appearance and finish.
The process ensures optimal performance and appearance of the produced parts by tightly controlling each step.
Soundproof booth’s laser cutting, which utilizes high-precision technology to provide fine and intricate cuts.
Bending to shape materials to meet design requirements, and welding to fuse different metal parts together to create a strong structure.
Polishing is the process of grinding and smoothing metal surfaces to improve their appearance and finish.
The process ensures optimal performance and appearance of the produced parts by tightly controlling each step.
5.External Sprayer Paint:
Cheerme office pod surfaces undergo spray painting treatment to improve both their aesthetic appeal and durability.
Booth’s external sprayer paint is a critical step for ensuring the appearance and long-term durability of the product. It involves the following sub-steps:
Oil and Rust Removal, which ensures adhesion of the coating by thoroughly removing oil, grease, and rust from the metal surface prior to spraying.
Pre processing of phone booth, which chemically treats the metal surface to improve corrosion resistance and adhesion of the coating.
Spray Primer is applied to provide a uniform base for the topcoat and enhance protection.
The spray topcoat applies the outermost layer of paint to provide color and an additional layer of protection.This stage is critical for phone booth's visual appeal and long-term protection. We use environmentally friendly, weather-resistant coatings to ensure the product maintains its appearance in various environments.
Booth’s external sprayer paint is a critical step for ensuring the appearance and long-term durability of the product. It involves the following sub-steps:
Oil and Rust Removal, which ensures adhesion of the coating by thoroughly removing oil, grease, and rust from the metal surface prior to spraying.
Pre processing of phone booth, which chemically treats the metal surface to improve corrosion resistance and adhesion of the coating.
Spray Primer is applied to provide a uniform base for the topcoat and enhance protection.
The spray topcoat applies the outermost layer of paint to provide color and an additional layer of protection.This stage is critical for phone booth's visual appeal and long-term protection. We use environmentally friendly, weather-resistant coatings to ensure the product maintains its appearance in various environments.
6.Assembly:
Cheerme office pod is assembled from components according to precise craftsmanship standards.
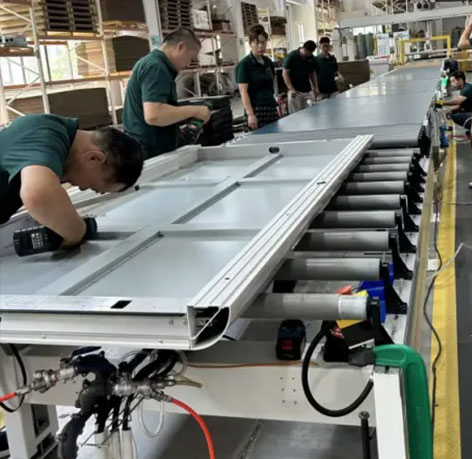
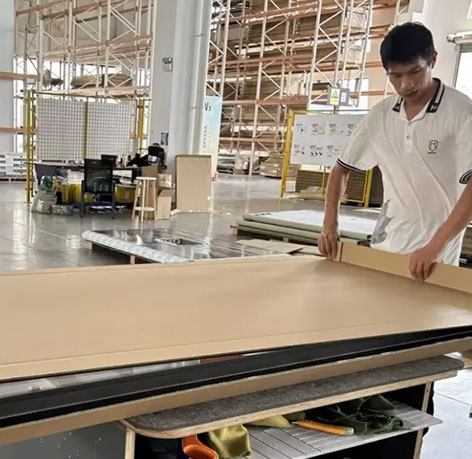
7.Finished Product Sampling:
To verify quality and compliance, Cheerme office booth undergo random sampling.
Finished phone booth sampling is the final quality assurance step in the production process. It involves taking random samples of finished products and subjecting them to quality checks, such as dimensional accuracy, functionality tests, and durability checks. This step ensures that every batch of products meets or exceeds customer expectations and industry standards.
Finished phone booth sampling is the final quality assurance step in the production process. It involves taking random samples of finished products and subjecting them to quality checks, such as dimensional accuracy, functionality tests, and durability checks. This step ensures that every batch of products meets or exceeds customer expectations and industry standards.

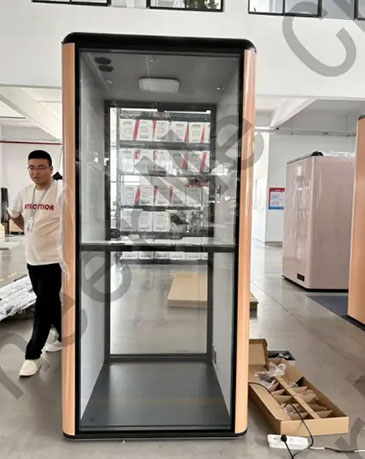
8.Packing:
Cheerme qualified office booth are packaged to ensure their protection during subsequent logistics processes.
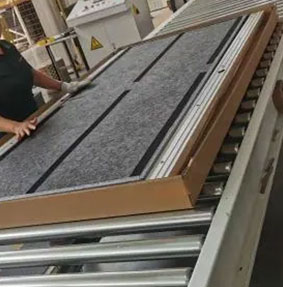
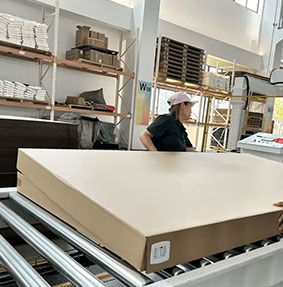
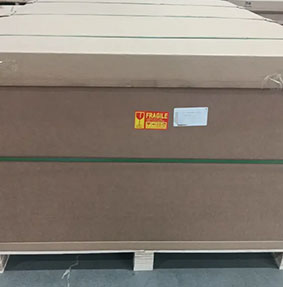
9.Warehouse:
Our office booth factory’s warehouse stores packaged products that are ready for distribution to various sales outlets.
10.Final Testing:
Before leaving the factory, all office booth undergo comprehensive performance and safety tests.
11.Shipping:
We dispatch rigorously tested products worldwide to reach our customers.
Shipment Inspection Specifications and reports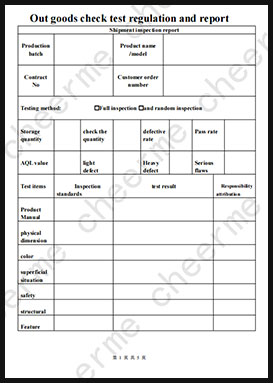
Office Booth Material Check Test Regulation and Report
In-Depth Analysis of Phone Booth Raw Material Inspection Process
Shipment Inspection Specifications and reportsIn manufacturing, the quality of raw materials directly affects the final product. Raw Material Inspection is crucial to ensure product quality. By inspecting Cheerme 1 to 6 office booth raw materials precisely, we can prevent substandard materials from entering production, laying the foundation for high-quality products. This article will discuss the main aspects of raw material inspection, including inspection methods, processes, and record management. These elements work together to ensure the product's consistent high performance.
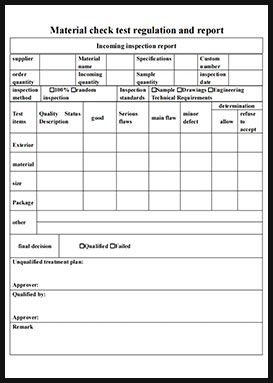
Selection and Execution of Inspection Methods for Office Booth Raw Materials
The inspection of raw materials relies on a series of meticulously selected and designed methods for different types of materials.
Visual Inspection:
The purpose of this inspection is to ensure that the raw materials meet the preset standards for appearance without any visible defects, such as cracks, rust, or other surface imperfections.
This inspection is carried out using various methods. The process usually includes examining the item visually, assessing it by touch, and comparing it to a sample.
This inspection is carried out using various methods. The process usually includes examining the item visually, assessing it by touch, and comparing it to a sample.
Dimensional Inspection:
The purpose of dimensional inspection is to ensure the accuracy of raw materials, meeting production requirements. This is typically achieved by using measuring tools such as calipers, micrometers, tape measures, rulers, dial indicators, plug gauges, and platforms for verification.
Structural Testing:
Evaluates the strength and durability of office booth raw materials.
Tensioners, torquers, and pressure gauges are commonly used for verification.
Tensioners, torquers, and pressure gauges are commonly used for verification.
Characteristic Testing:
The purpose of this test is to evaluate the electrical, physical, chemical, and mechanical properties of raw materials to ensure they meet production and product performance requirements.
These tests are typically conducted using specialized instruments and specific methods.
These tests are typically conducted using specialized instruments and specific methods.
Inspection Process Details:
The raw material inspection process is systematic and standardized. The following are the key steps:
Establishment of Inspection and Testing Specifications:
Quality engineers create inspection and testing specifications and work instructions based on the type and characteristics of raw materials.
These specifications and instructions must be approved by the manager and distributed to inspectors for execution.
These specifications and instructions must be approved by the manager and distributed to inspectors for execution.
Preparation for Inspection:
The purchasing department notifies the warehouse and quality department to prepare for receipt and inspection based on the arrival date, type, specification, and quantity.
Execution of Inspection:
Upon receiving the inspection notice, inspectors carry out the inspection according to the specifications, filling in the inspection record and daily report.
Marking of Qualified Materials:
Qualified Materials are marked after passing inspection. Procurement and warehouse personnel are then notified to proceed with storage procedures.
Emergency Release Procedures:
Follow emergency release procedures if raw materials are urgently needed for production and there is no time for inspection and testing.
Non-conforming Materials Handling:
In case of non-conforming materials identified during inspection, promptly fill out the 'Product Inspection Non-conforming Product List'. The quality engineer will confirm and provide reference opinions, submitting them to the manager for handling.
Inspection Records Management:
The quality department clerk collects inspection records daily. After compiling and summarizing the data, they organize it into a booklet for future reference and keep it properly according to the specified period.
Through the inspection process outlined above, we ensure that every batch of raw materials undergoes quality control, providing a foundation for high-quality final products. Raw material inspection is not just the starting point of quality control; it's a crucial part of our commitment to quality. We ensure that every raw material batch lays the foundation for manufacturing the highest quality products through precise controls and relentless efforts.
Through the inspection process outlined above, we ensure that every batch of raw materials undergoes quality control, providing a foundation for high-quality final products. Raw material inspection is not just the starting point of quality control; it's a crucial part of our commitment to quality. We ensure that every raw material batch lays the foundation for manufacturing the highest quality products through precise controls and relentless efforts.
Office Pods Equipment Testing Process and Acceptance Criteria
Cheerme plants ensures that the appearance, structure, and performance of the office pods meet specification requirements and customer expectations. It serves as a quality reference for sample signing. Below we will clarify the main aspects of these standards, such as surface grade classification, defect classification, and inspection environment and tool requirements.
Office Pods Quality Inspection Standard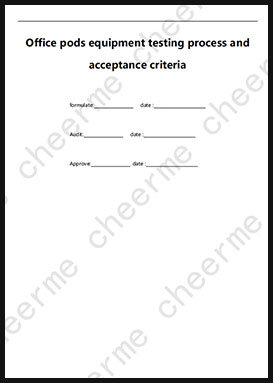